- Joined
- Feb 25, 2010
- Messages
- 1,643
- Points
- 113
HMMMMM ??? What other group of Technology / Users is obsessed with heat removal ....Overclockers !!! SO...I will see what they say ????? Aside from Liquid Nitrogen cooling.....For starters.....They seem to like this fan......
SO....High Static Pressure is mentioned. I will continue to investigate and study what the Overclocker group sez........Obviously....this is a huge area !!!
….and I am truly a Stranger....in a Strange Land !!!
Bob
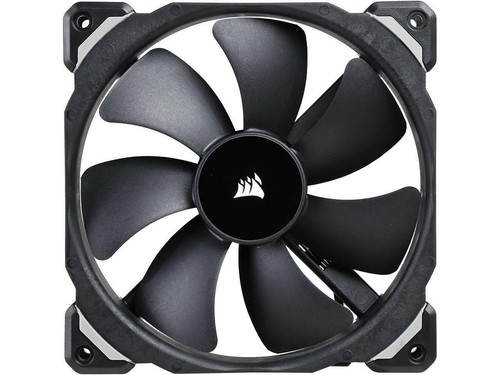
Corsair ML140 PRO CO-9050045-WW 140mm Premium Magnetic Levitation PWM Fan - Blac 843591072151 | eBay
Find many great new & used options and get the best deals for Corsair ML140 PRO CO-9050045-WW 140mm Premium Magnetic Levitation PWM Fan - Blac at the best online prices at eBay! Free shipping for many products!
www.ebay.com
SO....High Static Pressure is mentioned. I will continue to investigate and study what the Overclocker group sez........Obviously....this is a huge area !!!
….and I am truly a Stranger....in a Strange Land !!!
Bob