- Joined
- Dec 27, 2011
- Messages
- 2,062
- Points
- 48
Just a point of input: all of this speculation is based on how long we can keep the laser on before we have to turn it off. That's all fine and dandy - maybe nickel really will help with the amount of time a laser can be kept on. However, we also know that it will drastically increase the amount of time it must be kept off before it can be turned on again for another full duty-cycle.
The question: is that what you want? For my builds, I prefer shortish duty-cycles (45 seconds-60 seconds on) with 30-45 seconds off. That's why I typically use copper when I can - it aids in transfer to the host a lot more than anything else (especially when getting a tight fit to the host), thus allowing it to dissipate that heat faster and be able to be turned on more quickly.
Well...
That depends on whether there is more sink-to-air transfer going on than is being given credit.
I am working on this right now...
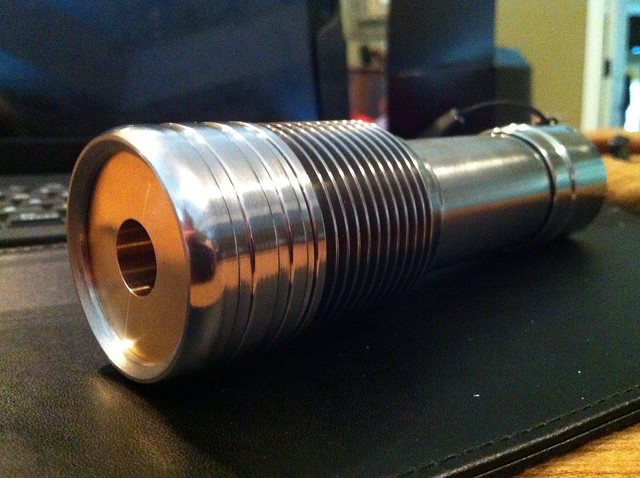
Awesome by tsteele93, on Flickr
It has the sink up front connected to a finned head (albeit stainless steel) that may dissipate more heat than we are giving the hostor credit for in this thread.
Here is my take, I think that copper is best. I'm curious about RHD's theory/questions. I think it would be intersting to see how nickel and stainless perform.
It isn't as complicated as some are trying to make it out to be. A simple test of identical sinks in a common host or two with binned diodes or the same diode in a copper module (which we all agree with offer a very good conduit to the various hosts - hopefully no one disagrees with this,) should show us if one metal stands out at keeping the diode cooler.
Last edited: