Apparently no one after likevvii posted spot pictures of 31T in this thread.
So I bought a new 31T from ebay and tested each row one by one using same ice cooled small tank, which I made for testing Osram chip earlier. Used same contacts in order to avoid soldering to chip wires directly.
The millimeter paper of today is bad, so I made more contrast lines with a pencil!
Here unlike in Osram chip all rows show spots of the same square shape at 5 m distance (0.5A current), and all LDs together show a similar square spot which fits into a 50x50 mm square. The spot even looks to be of 40x40 mm size. This square shape says to me that this thing was made for focusing and cuting.
I connected the rows as 2S2P (2 goups of 2 rows in series, it needed longer wires than with Osram chip, where the polarities apparently were designed for 2S2P), but first surprise:
BST400 DC booster driver which delivered 4A at 52V for Osram here could make maximum 5.7A at 40V with 24V input and its fuse became super hot...
Anyway BST400 delivered just a little less than I wanted to reach: 6A that would make 3A curent through each LD.
So here was the limit of my old driver and other cheap drives coming from ali could not make better - even BST-900W, which reference I posted in post 140 of this thread.
So it took some time to get a new bench power supply CPS-8412 which can deliver 6A at 42V easily.
Once focused by the PCV lens the spot at 20 cm looks to be 2x2 mm by size and at 6A cuts easily in 3 seconds (I could not check faster) through stainless steel 0.4-0.5mm thick. 5 or 10 seconds just make bigger holes. All time I had some ice in pot to keep the chip at room temperature or lower.
Moving the spot produces a pretty fast cut.
For comparison the holes made by Osram chip are above and are bigger due to worse focus and bigger spot, it also took more seconds to cut through.
On the left there is a spot left by H1650 block - which has a very bad focus at all.

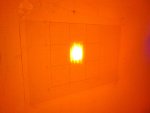
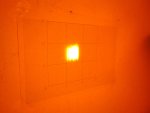
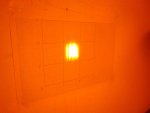
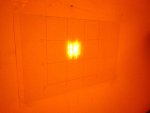
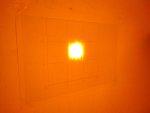

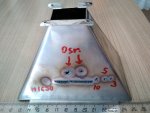
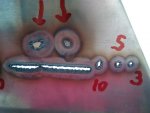