dunkelheit_phoenix_2008
Member
- Joined
- Dec 8, 2020
- Messages
- 70
- Points
- 8
Giannis, that's the signal of the totem pole, it's not the signal of the buck converter.All I can say is that I already consider the diode that you will buy dead. Also, you don't need to compare anything, I have designed multiple actual drivers and there is so much that you have gotten wrong about everything that is not even funny anymore... But first I want to point out: you said that "LM311 turns on and off your diode" So I say look at your waveform:![]()
I have marked the dead zones where the voltage of your converter drops to the 0 mark which is essentially turning off and on the diode. Then 40khz Is way way way too low, You will need a lot more output caps and also learn how to use a scope, To measure the ripple and get a proper waveform out of an SMPS converter you need to select AC coupling for your channel.... And finally, NOBODY HERE USES 311s FOR POWERING DIODES!
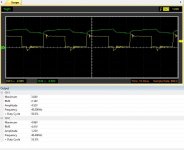
This is the signal of the step down, I already mention LM311 and LM317 just to point the difference vs DC-DC converters.