I am trying to set my current for my M-140. Im using an x-boost driver, connected to the diode on the - side, on the + side i have my DMM between the doide and the driver. I have the driver wired to a RCR123a battery.
So far, I have only seen it get past 1.0 once on the DMM, and I have turned the pot both ways several times and it doesnt seem to want to go any higher (it fluctuates down to about .4a at the lowest). Whats the problem here?
FWIW, the DMM red cord is plugged into the 10A port, and Im using in on the 10A option...
Edit: Here are some pictures of how I have it set up. I also have a test load I built, but straight out of the gate it was giving me readings I didnt find consistant with the driver specs, so I figured it was wrong. It was saying like 2.6A right when i turned it on, and on cajun lasers it says the max is 2.2A.
Here is the test load, its 6 diodes N4001, and a 1-kohm, 1 watt resistor.
So far, I have only seen it get past 1.0 once on the DMM, and I have turned the pot both ways several times and it doesnt seem to want to go any higher (it fluctuates down to about .4a at the lowest). Whats the problem here?
FWIW, the DMM red cord is plugged into the 10A port, and Im using in on the 10A option...
Edit: Here are some pictures of how I have it set up. I also have a test load I built, but straight out of the gate it was giving me readings I didnt find consistant with the driver specs, so I figured it was wrong. It was saying like 2.6A right when i turned it on, and on cajun lasers it says the max is 2.2A.
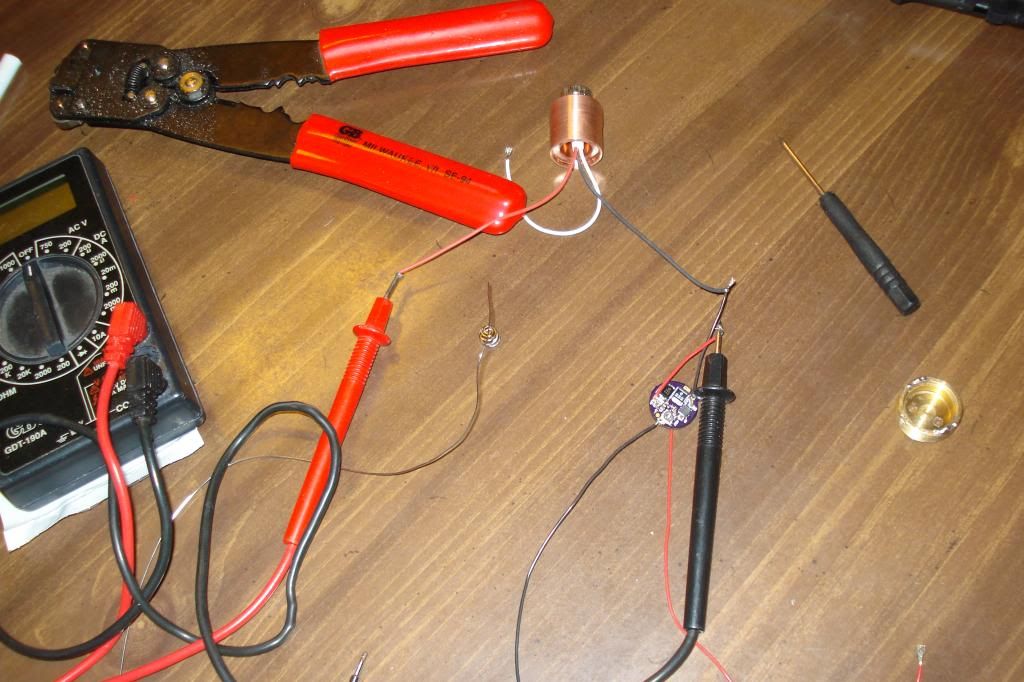
Here is the test load, its 6 diodes N4001, and a 1-kohm, 1 watt resistor.
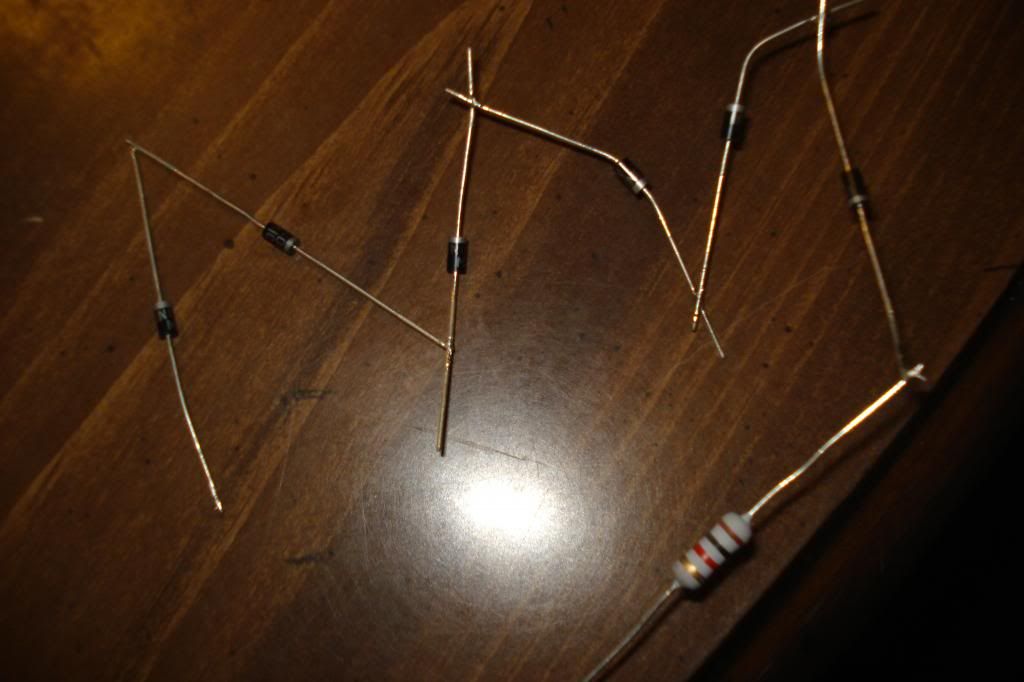
Last edited: