- Joined
- Jun 23, 2010
- Messages
- 14
- Points
- 0
Alright guys, I have an idea for a little project. I'm thinking of turning an old Maglight below into a quad laser. In other words, I'm thinking of utilizing the large space area of the head of the light to house 4 laser diodes. The length of the shaft (including removing some plastic crap around the on/off button leave me with more than enough room to house individual drivers, switches, and a rechargeable power source... or so I theorize.
As for the diodes, I'm thinking of spending the extra cash and going for the goods including...
- 300mW 650nm Red
- 150mW 405nm Blu Ray
- 150mW 532nm Green
- 1W (probably tuned down) 445mW Blue
Judging by the space within the head, I can imagine fitting a CNC cut aluminum disk measuring roughly around 2.5" in diameter and .75" deep (rough estimates by sight) as a heat sink and holder for the diodes. The area where the fill plastic for the main on/off button should be around 1.75" diameter and 3" deep (not including the battery area.
What I'm working with...
MY QUESTIONS:
1. Has anyone done such a setup before?
2. Would I run into a problem running a single voltage source? I was thinking a 6V rechargeable battery I haven't yet worked that out.
3. Other than heat, are there any problems I might face having 4 diodes within the same heat sink?
Thanks guys. This would be my first build, but I'm not new to electronics.
As for the diodes, I'm thinking of spending the extra cash and going for the goods including...
- 300mW 650nm Red
- 150mW 405nm Blu Ray
- 150mW 532nm Green
- 1W (probably tuned down) 445mW Blue
Judging by the space within the head, I can imagine fitting a CNC cut aluminum disk measuring roughly around 2.5" in diameter and .75" deep (rough estimates by sight) as a heat sink and holder for the diodes. The area where the fill plastic for the main on/off button should be around 1.75" diameter and 3" deep (not including the battery area.
What I'm working with...
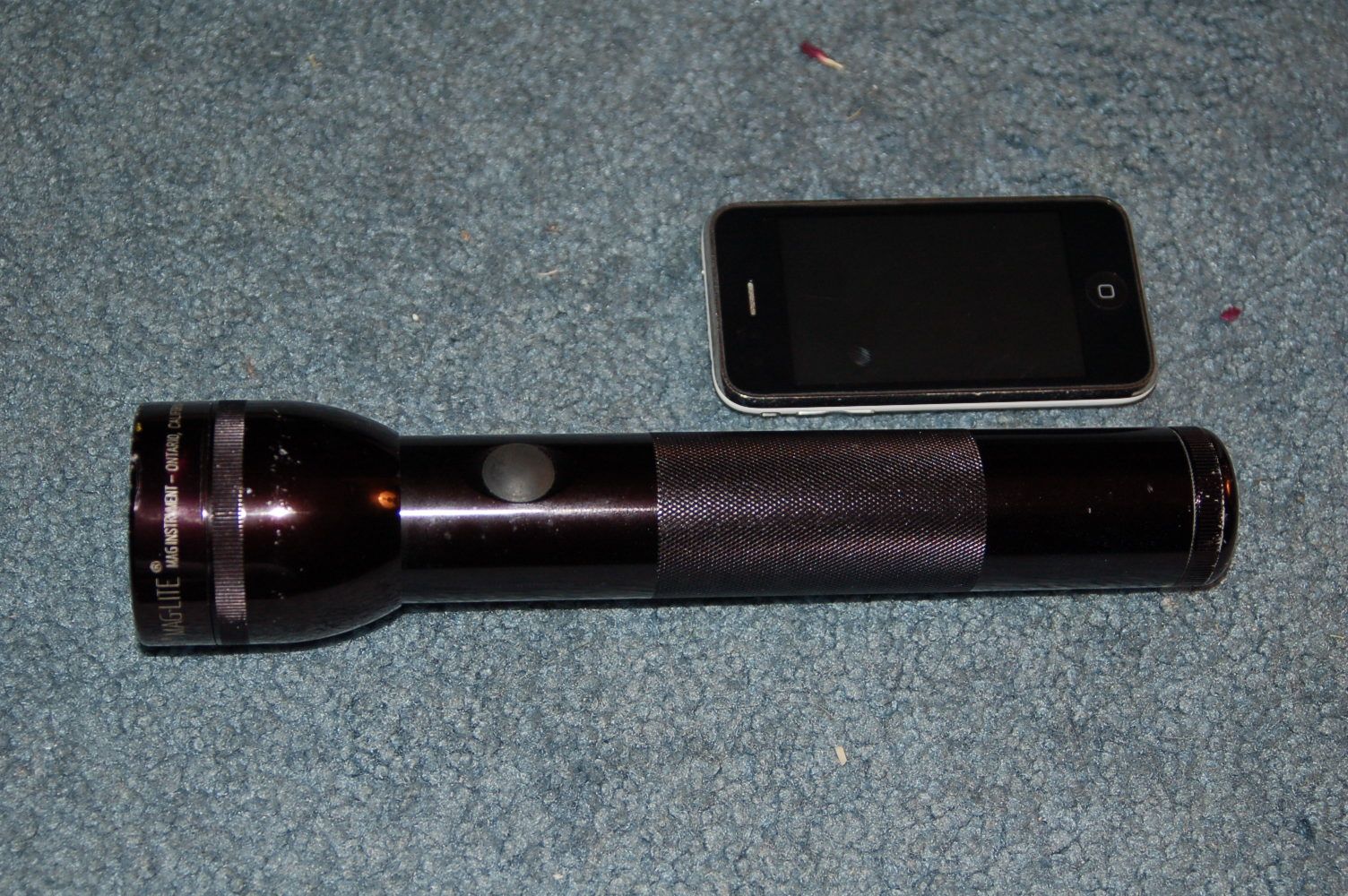
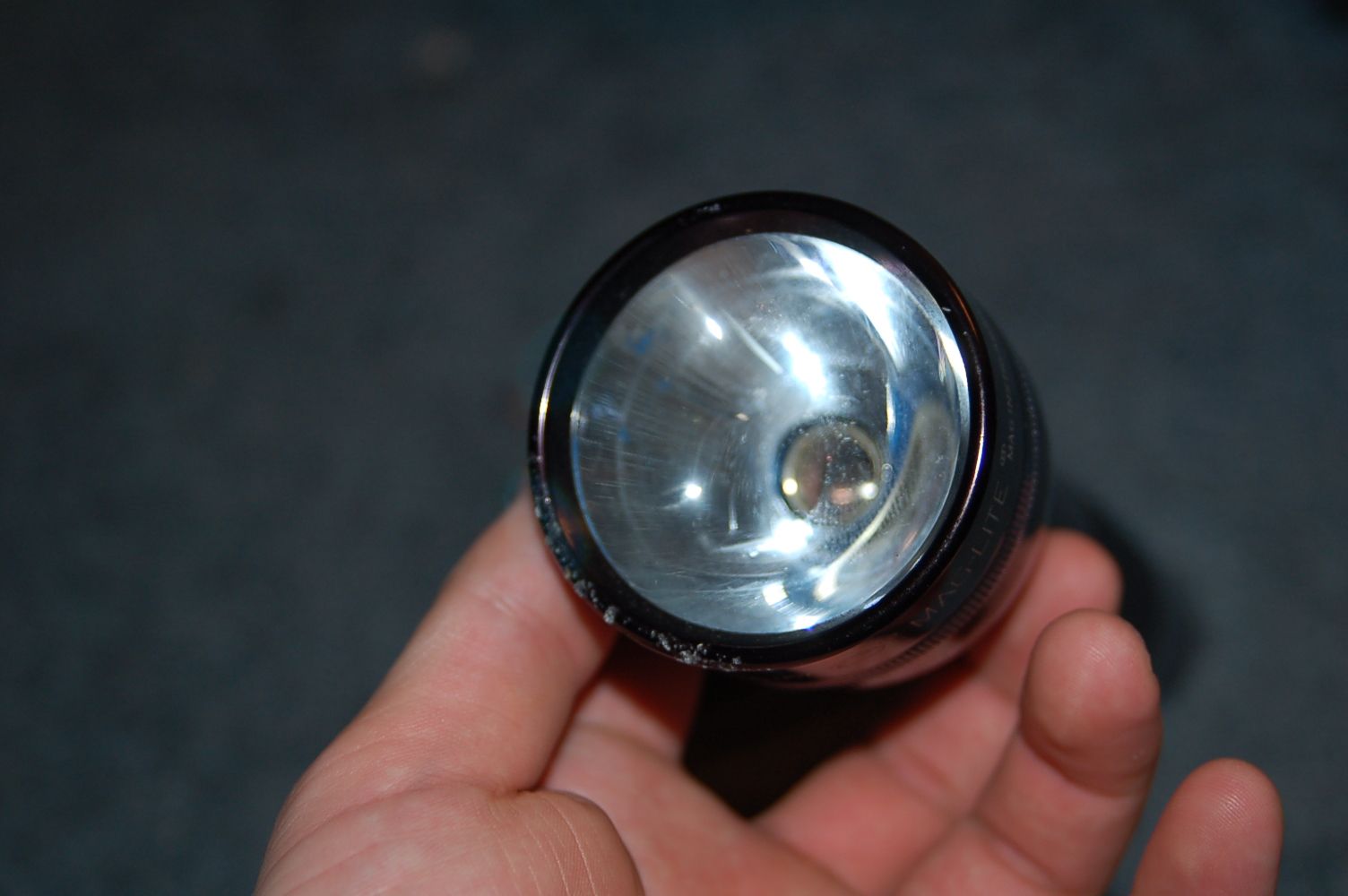
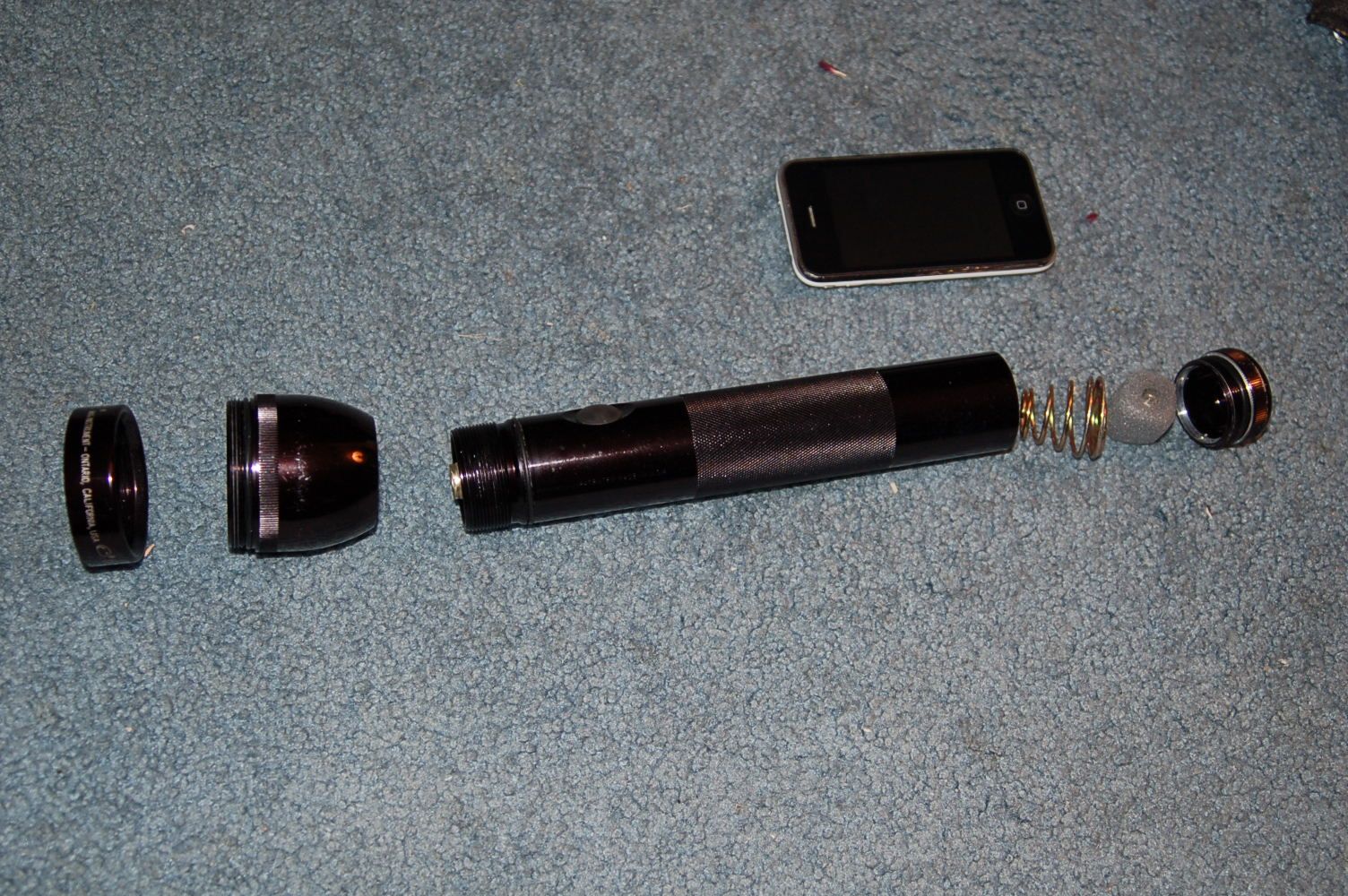
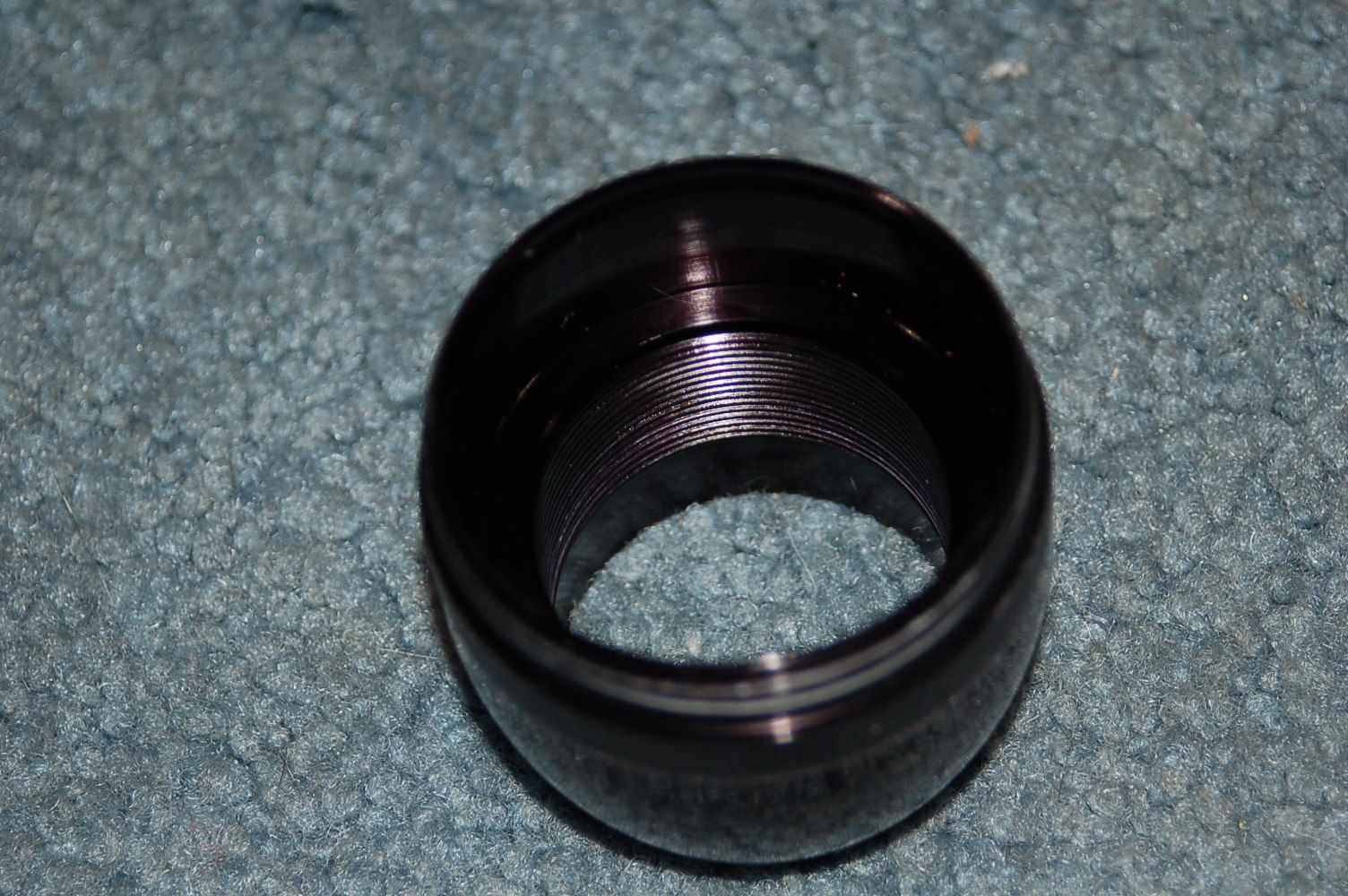
MY QUESTIONS:
1. Has anyone done such a setup before?
2. Would I run into a problem running a single voltage source? I was thinking a 6V rechargeable battery I haven't yet worked that out.
3. Other than heat, are there any problems I might face having 4 diodes within the same heat sink?
Thanks guys. This would be my first build, but I'm not new to electronics.