Hello Guys!
I got my RGB Pointer and my Cryo Laser done. So I was searching for a new project.
Turns out you need fog to see beams well. Who would have known...
I was using a vaping device to produce fog before. First (while I was still smoking) it was very convenient. However I quit smoking and needed an alternative.
I modified the vape stick to include a fan that draws the air trough it. It worked but it was very messy, liquid dripping everywhere. I could not stand this anymore so I decided to build something better.
Born was the idea of a hand held smoke machine that uses 18650 cells and does not produce a mess.
I started by choosing a pump and thinking about a heater block.
I decided I would use a small cheap peristaltic pump and heating cartridges out of a 3D printer.
The heaters are designed for 12V @70W, I wanted to keep the form factor small and only use 2 18650 cells.
So I used two 12V/70W cartridges to get around 65W heating with a full charge and around 50W while empty.
I milled my first heater block and tested everything with just DC at the heaters and a syringe as a "pump".
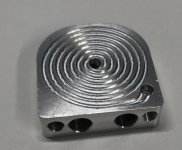
First tests where promising, way more fog that anticipated. Fogging up a small room to "cant see shit" took just about 5 minutes.
So I made up some PCBs and waited for them to get shipped:
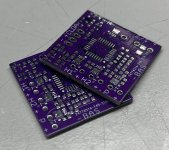
Looking quite nice already. I started the assembly process:
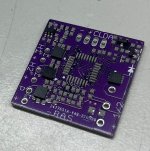
First, using a laser cut stencil, solder paste gets printed on the PCBs.
Components are placed on top off the wet paste.
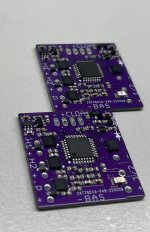
With everything placed, the pcb gets heated to solder temperature using a hot air gun. The paste melts and fixes the parts on the PCB.
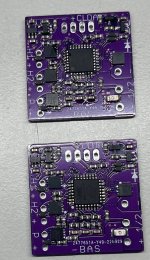
I needed to touch up some spots. I will clean that later. Next, the bottom side gets its paste printed and the parts placed.
A little soldering later, there are also some THT parts that need manual soldering.
Everything done:
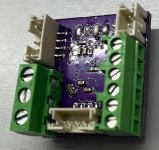
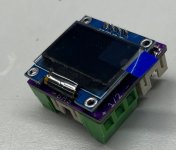
With the display soldered. Everything else gets connected:
- fire button with led for heating/ready
- encoder for menu navigation
- heating cartridges
- pump
- battery holder
- temp sensor
- finished heater block
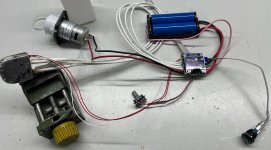
Adding some software trough that extra ribbon cable shows that everything works as intended.
Just a little programming is left to do. I want to regulate the pump to very slow speeds. This is necessary to control the fog volume.
The menu structure makes everything adjustable.
I currently have set up:
- Controlling the fog amount (pump speed)
- setting the temperature and saving it
- different modes (continues - manual - interval with adjustable times)
- battery under discharge protection
- sensor fault detection
(quite hard to take a picture of the oled screen) I am a german native speaker, thats why the menu is in german.
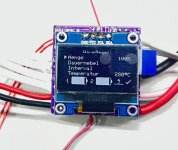
The board reads each battery state separately, this provides a safe way to determine the state of the battery.
If the battery gets close to over discharge, the board will disable one heater to limit the power draw and extend the runtime.
Some time later, the battery will be completely empty and the board will switch itself off.
A press on the fog button will turn it back on.
There is also a standby timer running. If the machine is idle and the standby time is up, the board will also turn itself off.
The display shows (bottom right) if both or just one heater is currently heating and if the set temperature is reached.
I still want to include some stuff like:
- regulating pump speed down if temperature gets too low, currently the pump just gets switched off
- adding a proper PID controller for the pump speed. I will use BackEMF to control the brushed DC motor
And a last picture showing some fog. Again hard to photograph. I will make proper pictures of the fog output later, this picture does not tell the whole story.
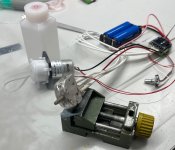
Now I need to finish the software and get a case done.
Keep you updated.
I got my RGB Pointer and my Cryo Laser done. So I was searching for a new project.
Turns out you need fog to see beams well. Who would have known...
I was using a vaping device to produce fog before. First (while I was still smoking) it was very convenient. However I quit smoking and needed an alternative.
I modified the vape stick to include a fan that draws the air trough it. It worked but it was very messy, liquid dripping everywhere. I could not stand this anymore so I decided to build something better.
Born was the idea of a hand held smoke machine that uses 18650 cells and does not produce a mess.
I started by choosing a pump and thinking about a heater block.
I decided I would use a small cheap peristaltic pump and heating cartridges out of a 3D printer.
The heaters are designed for 12V @70W, I wanted to keep the form factor small and only use 2 18650 cells.
So I used two 12V/70W cartridges to get around 65W heating with a full charge and around 50W while empty.
I milled my first heater block and tested everything with just DC at the heaters and a syringe as a "pump".
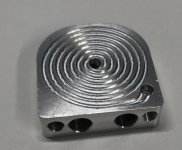
First tests where promising, way more fog that anticipated. Fogging up a small room to "cant see shit" took just about 5 minutes.
So I made up some PCBs and waited for them to get shipped:
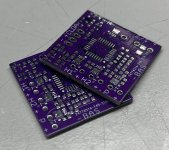
Looking quite nice already. I started the assembly process:
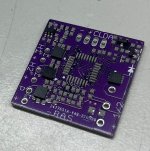
First, using a laser cut stencil, solder paste gets printed on the PCBs.
Components are placed on top off the wet paste.
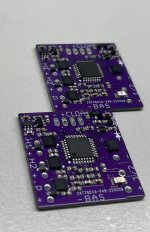
With everything placed, the pcb gets heated to solder temperature using a hot air gun. The paste melts and fixes the parts on the PCB.
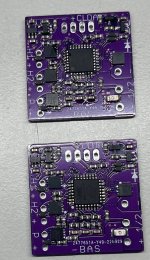
I needed to touch up some spots. I will clean that later. Next, the bottom side gets its paste printed and the parts placed.
A little soldering later, there are also some THT parts that need manual soldering.
Everything done:
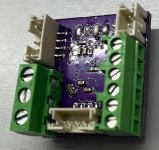
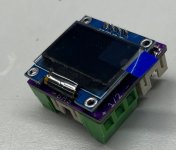
With the display soldered. Everything else gets connected:
- fire button with led for heating/ready
- encoder for menu navigation
- heating cartridges
- pump
- battery holder
- temp sensor
- finished heater block
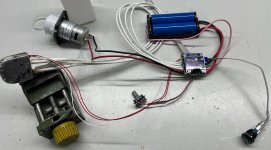
Adding some software trough that extra ribbon cable shows that everything works as intended.
Just a little programming is left to do. I want to regulate the pump to very slow speeds. This is necessary to control the fog volume.
The menu structure makes everything adjustable.
I currently have set up:
- Controlling the fog amount (pump speed)
- setting the temperature and saving it
- different modes (continues - manual - interval with adjustable times)
- battery under discharge protection
- sensor fault detection
(quite hard to take a picture of the oled screen) I am a german native speaker, thats why the menu is in german.
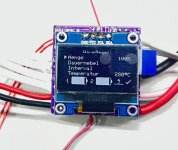
The board reads each battery state separately, this provides a safe way to determine the state of the battery.
If the battery gets close to over discharge, the board will disable one heater to limit the power draw and extend the runtime.
Some time later, the battery will be completely empty and the board will switch itself off.
A press on the fog button will turn it back on.
There is also a standby timer running. If the machine is idle and the standby time is up, the board will also turn itself off.
The display shows (bottom right) if both or just one heater is currently heating and if the set temperature is reached.
I still want to include some stuff like:
- regulating pump speed down if temperature gets too low, currently the pump just gets switched off
- adding a proper PID controller for the pump speed. I will use BackEMF to control the brushed DC motor
And a last picture showing some fog. Again hard to photograph. I will make proper pictures of the fog output later, this picture does not tell the whole story.
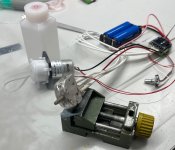
Now I need to finish the software and get a case done.
Keep you updated.
Last edited: