Fiddy
0
- Joined
- May 22, 2011
- Messages
- 2,736
- Points
- 63
G'day,
A question for someone in the know,
Im making my first PCB and im pretty much done but ive found what i think is a problem.
ive got a big polygon on each side of the board (GND is top ,12V+ is bottom) and when i connect pins to the polygon i get this cross-hair looking connection to the polygon, see this photo:
Is that normal to send of to get the boards made?
if not, how to i get a better connection like with other connections that arnt to a polygon?
Cheers! Fiddy.
A question for someone in the know,
Im making my first PCB and im pretty much done but ive found what i think is a problem.
ive got a big polygon on each side of the board (GND is top ,12V+ is bottom) and when i connect pins to the polygon i get this cross-hair looking connection to the polygon, see this photo:
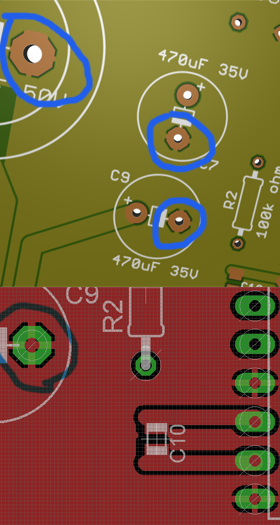
Is that normal to send of to get the boards made?
if not, how to i get a better connection like with other connections that arnt to a polygon?
Cheers! Fiddy.