- Joined
- Jun 24, 2010
- Messages
- 5,704
- Points
- 113
Due to a recent product review on an engraver head that the reviewer could not get to cut and engrave different materials at the rates advertised. I think there was an issue with the lens being contaminated during the testing but the reviewer did correctly call out an overstated power rating due to improper testing, and during the tear down revealed use of a DC-DC voltage regulator not a constant current laser driver which will severely affect the long term reliability of the product. These are produced with the NUBM44-V2 7W diodes in modules I supply but this company even without my endorsement were calling them 8W/10W/12W.
LPM testing that does not give any useful info and even can be deceptive is something I am seeing more and more which Is one of the first things I want to address since I have been dragged into this.
So hopefully to give understanding on from a buyers perspective on what to need to see before buying a laser and for sellers how to do the proper testing for full disclosure to their customers.
Hopefully this will start to cut though some of the confusing misconceptions that the many many followers of both parties were throwing out there. For the reviewer on Youtube subscribers and for the company on their own forum hosted on their website. The real issue was the original knee jerk reaction of the company(which it was a pretty devastating review) as the way he responded to the review which was very aggressive to say the least and caused a lot of twitter.
Also as far as I know the high power MM display diodes are not designed to be pushed very high running in pulsed mode but see a lot of these 12W/15W ect... being explained by running them in pulsed mode. If not designed for it even though you can do it does not mean it won't cause failure. Maybe the AR coating on the window can't handle it and burns up and that is just an example which there are many others. Bond wires might not be able to handle it, Could deweld the wires or even the dye, the cavity could receive great shock damage ect....
To start here is the correct way to do a power test of finished laser. A picture is useless and more likely can be used to deceive and a test video where you just get to the peak and turn it off also is not very useful unless you are saying ti can only run that long before you have to turn it off to cool the laser. Here is an example of worthless as I can make a NUBM44-V2 show 9W real for a spit second so the way tests are done now this is a 9W laser.
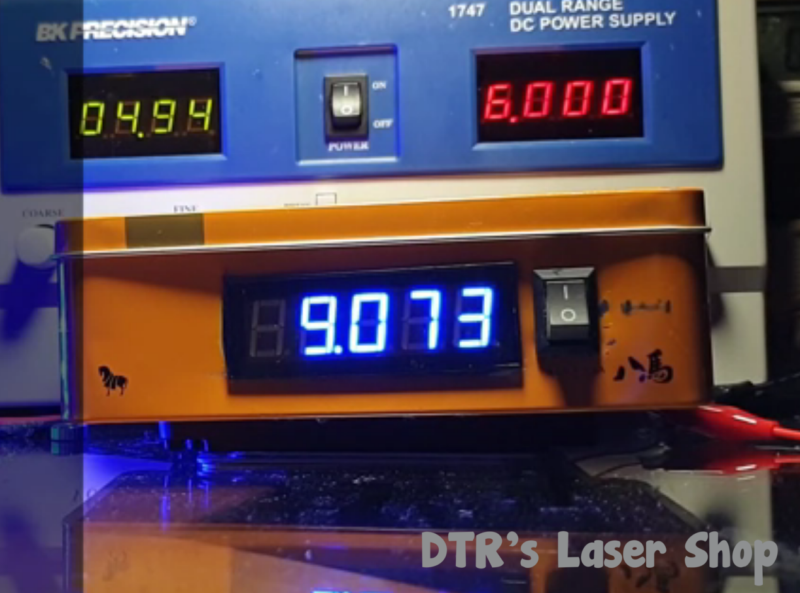
1. A proper test should be for the duration of the duty cycle if one is being stated to show that the laser can do what is claimed and the power that is being held. If offered with a claim of continuous operation then the test should be at least from power up to the point where the unit stabilizes. The rated power of the laser can be figured based on the average over this run.
2. The laser should not be close enough to the meters sensor that there is heat radiation from the laser interfering with the optical readings. Usually 4-6 inches between the two should be enough.
Here are some examples of the proper way to power test on a LPM. There are a lot of mist calibrated LPM's out there but even more important than than the max is the stability of the laser which even a out of calibration LPM will show. Or if the laser is not holding constant current and the readings don't slowly fall but go up as it runs this is a sign of a constant voltage power source which will cause significant reliability issues.
If you are not showing the stability of the laser under normal operating conditions then it is a waste of effort.
LPM testing that does not give any useful info and even can be deceptive is something I am seeing more and more which Is one of the first things I want to address since I have been dragged into this.
So hopefully to give understanding on from a buyers perspective on what to need to see before buying a laser and for sellers how to do the proper testing for full disclosure to their customers.
Hopefully this will start to cut though some of the confusing misconceptions that the many many followers of both parties were throwing out there. For the reviewer on Youtube subscribers and for the company on their own forum hosted on their website. The real issue was the original knee jerk reaction of the company(which it was a pretty devastating review) as the way he responded to the review which was very aggressive to say the least and caused a lot of twitter.
Also as far as I know the high power MM display diodes are not designed to be pushed very high running in pulsed mode but see a lot of these 12W/15W ect... being explained by running them in pulsed mode. If not designed for it even though you can do it does not mean it won't cause failure. Maybe the AR coating on the window can't handle it and burns up and that is just an example which there are many others. Bond wires might not be able to handle it, Could deweld the wires or even the dye, the cavity could receive great shock damage ect....
To start here is the correct way to do a power test of finished laser. A picture is useless and more likely can be used to deceive and a test video where you just get to the peak and turn it off also is not very useful unless you are saying ti can only run that long before you have to turn it off to cool the laser. Here is an example of worthless as I can make a NUBM44-V2 show 9W real for a spit second so the way tests are done now this is a 9W laser.
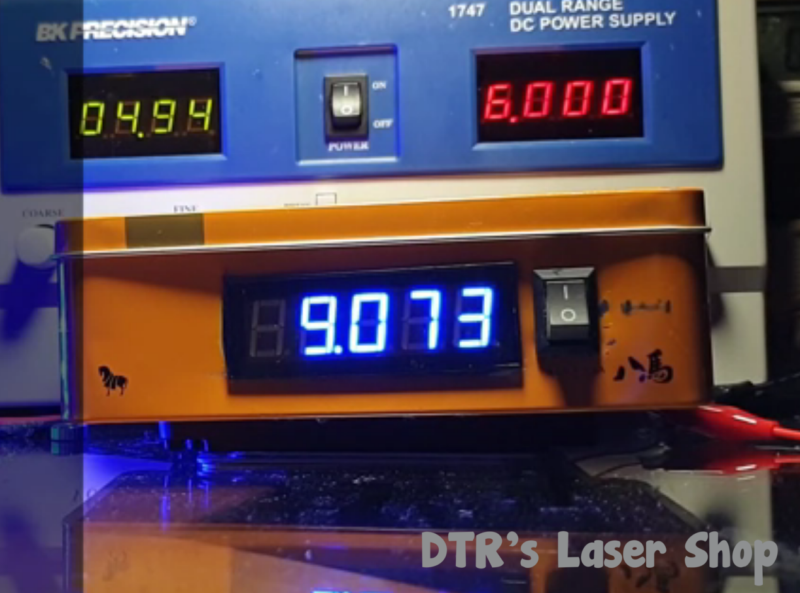
1. A proper test should be for the duration of the duty cycle if one is being stated to show that the laser can do what is claimed and the power that is being held. If offered with a claim of continuous operation then the test should be at least from power up to the point where the unit stabilizes. The rated power of the laser can be figured based on the average over this run.
2. The laser should not be close enough to the meters sensor that there is heat radiation from the laser interfering with the optical readings. Usually 4-6 inches between the two should be enough.
Here are some examples of the proper way to power test on a LPM. There are a lot of mist calibrated LPM's out there but even more important than than the max is the stability of the laser which even a out of calibration LPM will show. Or if the laser is not holding constant current and the readings don't slowly fall but go up as it runs this is a sign of a constant voltage power source which will cause significant reliability issues.
If you are not showing the stability of the laser under normal operating conditions then it is a waste of effort.
Last edited: