LightSourceBlue
New member
- Joined
- Sep 4, 2024
- Messages
- 24
- Points
- 3
I haven't had any experience with a lathe before, but after seeing a few posts from members here showing what they had some with theirs I did a bit of research and decided to try one. Will start our with doing a heatsink and then eventually might tackle doing a host. I have a Bambu X1C which is great for doing stuff with plastic but I really want to be doing more with metals - so feel like this is a good starting point.
I was fairly limited by space and weight requirement, I don't have a workbench so I needed to find an option which was small enough to fit in a cupboard and light enough to pick up and out away. This one is 12kg weight and length wise will just fit in the cupboard I need to store it on, chose the 80mm chuck option so feel like that will give me the most flexibility.
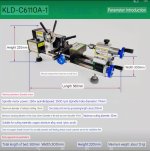
Any tips on working with a lathe like this? What am I realistically going to be able to do with this? Thinking of working with mostly softer copper and aluminium. The seller told me it can do all of this, but I'm still skeptical how well!
I was fairly limited by space and weight requirement, I don't have a workbench so I needed to find an option which was small enough to fit in a cupboard and light enough to pick up and out away. This one is 12kg weight and length wise will just fit in the cupboard I need to store it on, chose the 80mm chuck option so feel like that will give me the most flexibility.
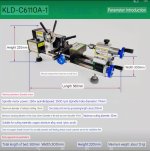
Any tips on working with a lathe like this? What am I realistically going to be able to do with this? Thinking of working with mostly softer copper and aluminium. The seller told me it can do all of this, but I'm still skeptical how well!