- Joined
- Jun 12, 2015
- Messages
- 7,678
- Points
- 113
One of the benefits of working in a school design technology department is that I have access to a range of materials and a co2 laser cutter. Also it helps being on good terms with the science department too. So I decided to run some experiments making crystals under laser conditions. The first crystal I was successful in producing was halite. So this set the course for something more ambitious.
I went to the science department and asked for some aluminium oxide (Al2O3) powder as well as trying my luck for some powdered dopants (Chromium, Titanium and Iron).
Out of the dopants however they only had iron powder. This did present a problem though. Iron powder of that purity is highly oxidising and presented a risk of a metal fire. And it also occurred to me that they are the ingredients used in thermite. So I went away empty handed at first.
After some thinking, I realised I had plenty of steel lying around. Steel as people know is a iron based alloy. I have lasered steel plenty of times before without issues. I was still nervous of lasering it in powdered form, but figured the contaminants would lessen the risk of drastic oxidisation. So I got myself some paper and a steel block, and began filing away creating steel dust.
The first step was to cut some 30-40mm aluminium squares and beat them to create a parabolic like dish.
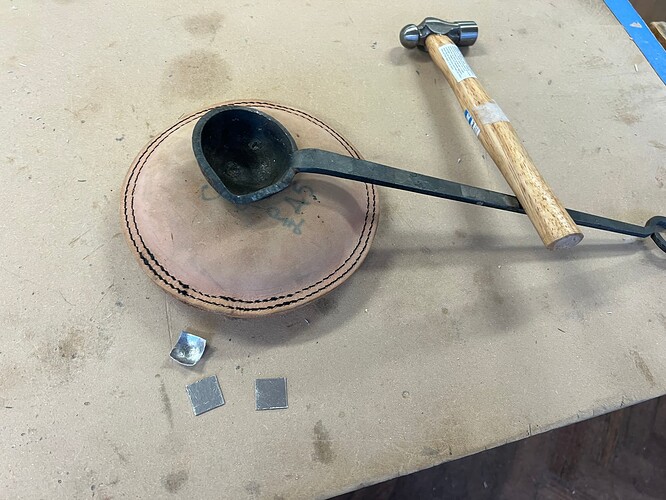
The next step was to put a small heap of aluminium oxide into the aluminium dish.
The idea was the parabolic shape would help focus some of the laser into a point within the medium. Aluminium is typically a reflector at IR wavelengths.
And then I sprinkled some steel dust on top.
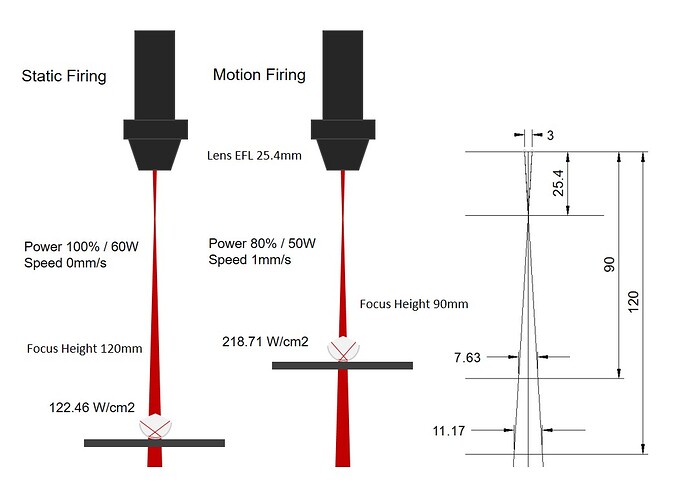
I tried static firing with the laser defocused to a focus height of 120mm first. Setting the laser to fire automatically runs at 100% power, which is 60W in this case. The focal length of the laser lens was 25.4mm and the beam diameter of a CO2 laser is typically around 3mm so I was able to estimate the spot size and therefore the intensity at this height.
This was the result of the first spot firings.
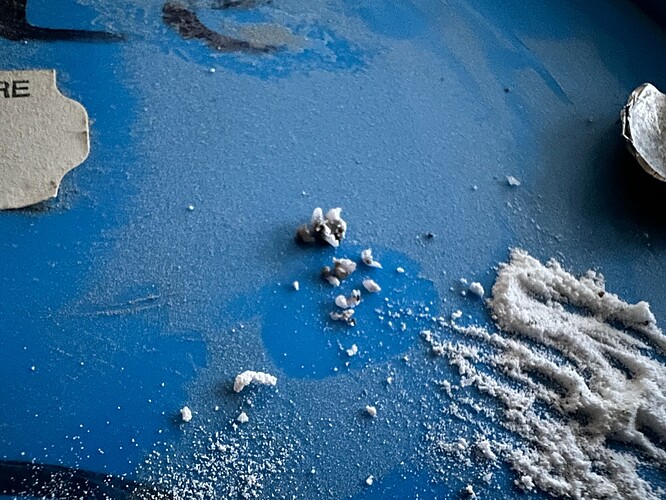
Bingo, corundum crystals!
What surprised me also was the production of ruby. Then I figured the steel I used must have been an old piece of stainless steel which contains chromium. Using a small 395nm torch I was able to fluoresce the ruby crystals further confirming them.
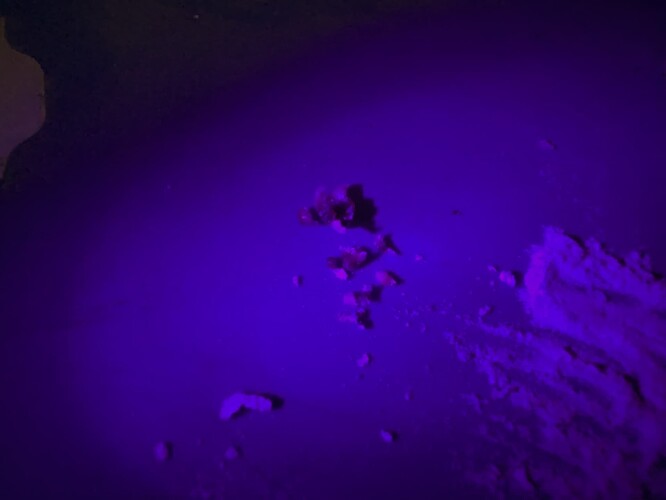
Now it was time to improve on things. The previous firing took a while to heat the aluminium oxide to exceed 2072°C that it needs to become molten. I decided to decrease the focal height to 90mm increasing the laser intensity.
This was the result:
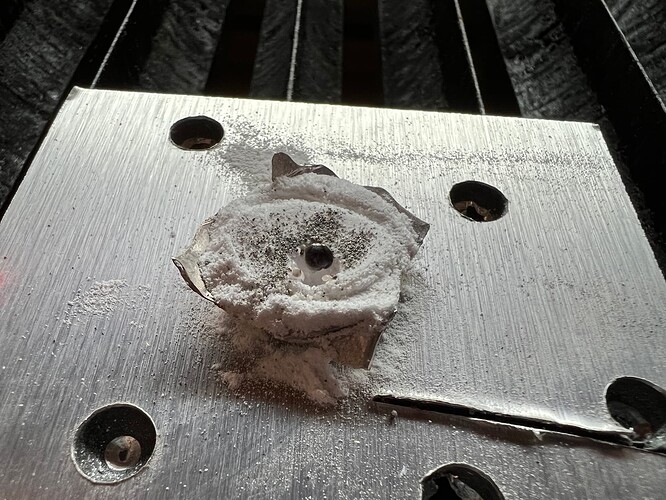
The result produced a single black sapphire and surrounding microcrystal of ruby.
After more runs I found that if I moved the laser head manually by a couple of mm whilst the aluminium oxide was still molten, I was then able quickly heat the surrounding powder and add to the previous crystal through coalescence. The coalescence was random and sometimes it contributed to the original crystal or it began forming a new one.
Once the aluminium oxide was hot enough I found it took very little to melt the surrounding oxide to the point I could now have a slow travelling beam.
So I adopted this 10mm square cut route. I set the laser to travel at 1mm/s at line intervals of 0.125mm.
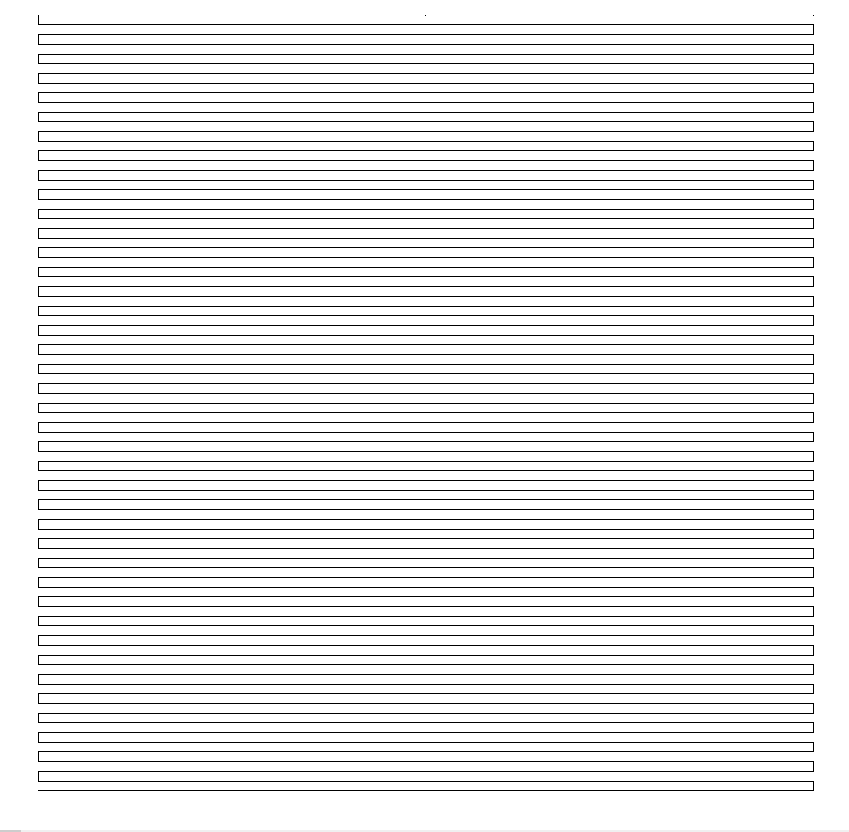
After a full pass I was able to gather a nice collection of rubies and sapphires.
I didn’t have time to get myself a sieve so the container contains some aluminium oxide powder as well.
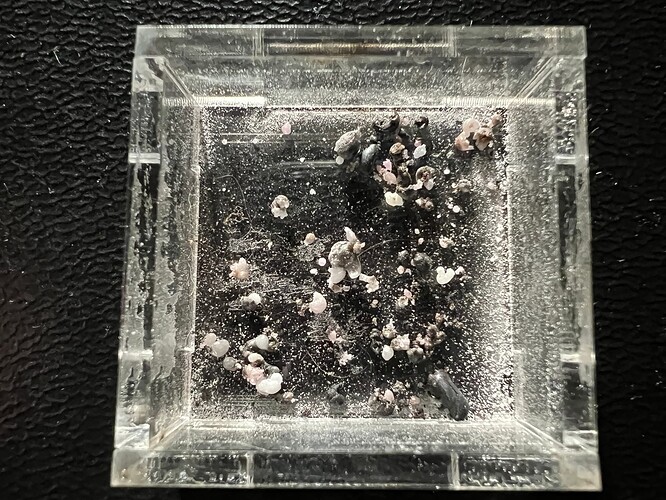
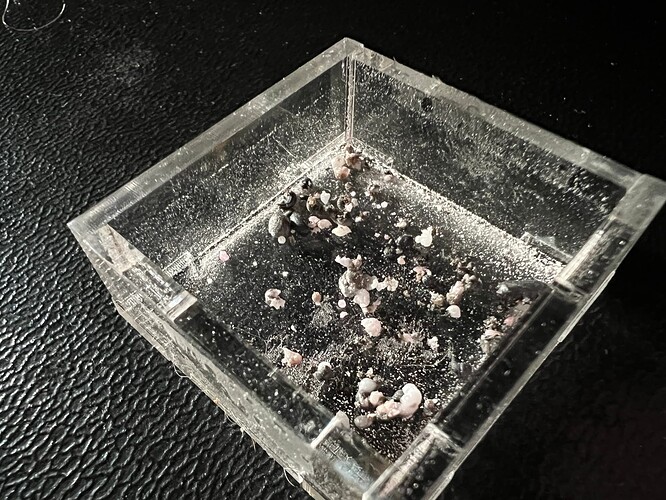
And now the fluorescence shots!
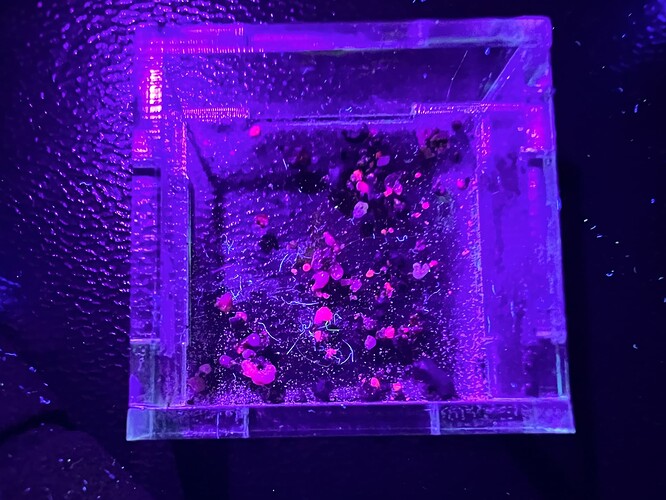
BA32DF41-15FB-490E-9F48-DE49D4D0E87A (1)1920×1440 235 KB
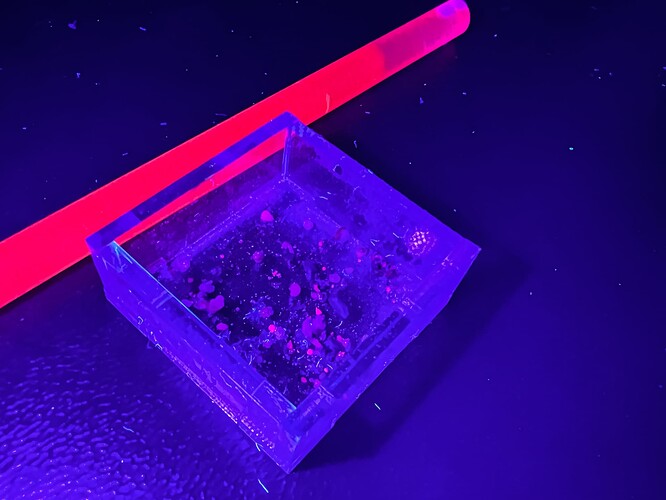
Using steel dust as a dopant produced some interesting results and potentially rare raw crystals. I have a couple of samples that have coalesced together containing ruby, clear sapphire and black sapphire. There also appears to be pale yellow variety present. I am yet to produce the classic blue sapphire.
To improve things further I am going to try a couple more things.
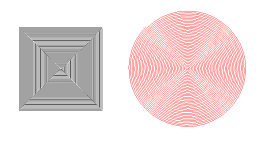
Edit:
Some closeups of some of the crystals.
And under closer inspection I have discovered at least two microscopic blue sapphires.
Note: The image has had to be altered to show the blue tint. It was very hard to capture it on my phone.
I went to the science department and asked for some aluminium oxide (Al2O3) powder as well as trying my luck for some powdered dopants (Chromium, Titanium and Iron).
Out of the dopants however they only had iron powder. This did present a problem though. Iron powder of that purity is highly oxidising and presented a risk of a metal fire. And it also occurred to me that they are the ingredients used in thermite. So I went away empty handed at first.
After some thinking, I realised I had plenty of steel lying around. Steel as people know is a iron based alloy. I have lasered steel plenty of times before without issues. I was still nervous of lasering it in powdered form, but figured the contaminants would lessen the risk of drastic oxidisation. So I got myself some paper and a steel block, and began filing away creating steel dust.
The first step was to cut some 30-40mm aluminium squares and beat them to create a parabolic like dish.
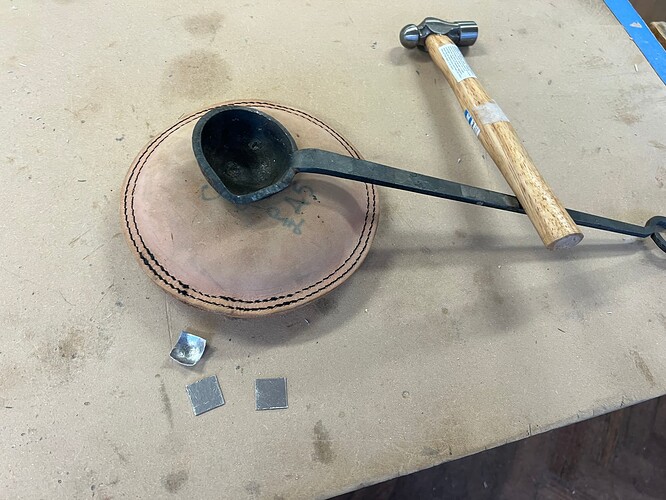
The next step was to put a small heap of aluminium oxide into the aluminium dish.
The idea was the parabolic shape would help focus some of the laser into a point within the medium. Aluminium is typically a reflector at IR wavelengths.
And then I sprinkled some steel dust on top.
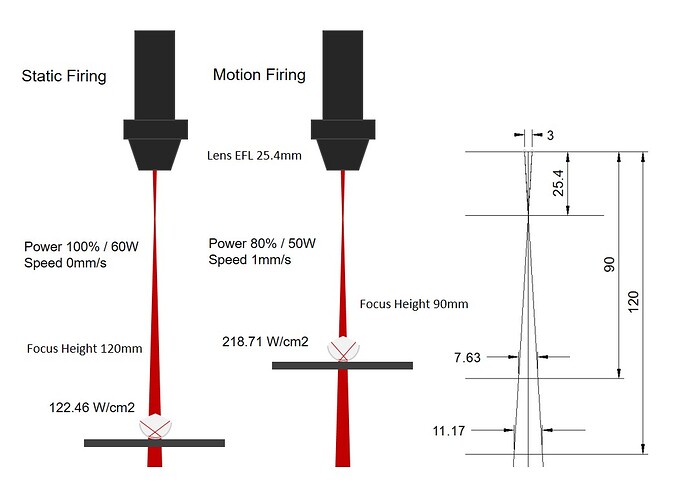
I tried static firing with the laser defocused to a focus height of 120mm first. Setting the laser to fire automatically runs at 100% power, which is 60W in this case. The focal length of the laser lens was 25.4mm and the beam diameter of a CO2 laser is typically around 3mm so I was able to estimate the spot size and therefore the intensity at this height.
This was the result of the first spot firings.
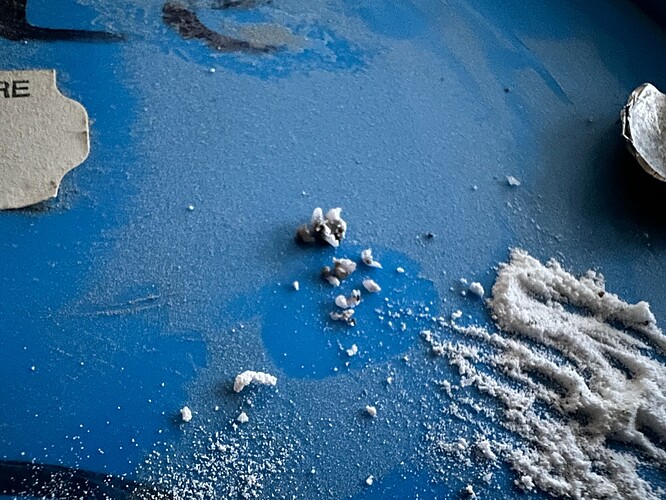
Bingo, corundum crystals!
What surprised me also was the production of ruby. Then I figured the steel I used must have been an old piece of stainless steel which contains chromium. Using a small 395nm torch I was able to fluoresce the ruby crystals further confirming them.
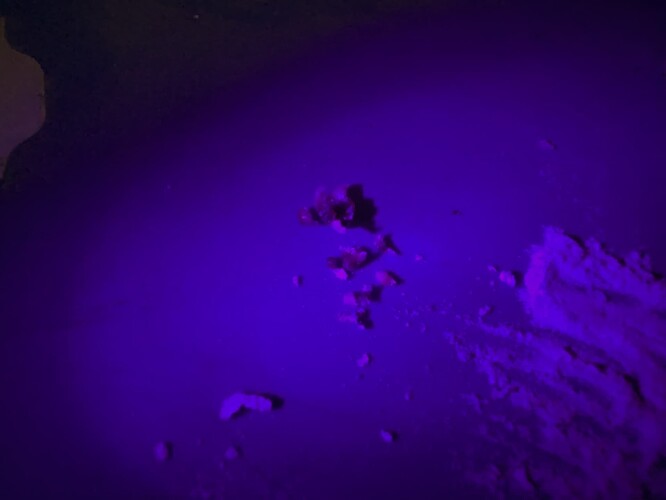
Now it was time to improve on things. The previous firing took a while to heat the aluminium oxide to exceed 2072°C that it needs to become molten. I decided to decrease the focal height to 90mm increasing the laser intensity.
This was the result:
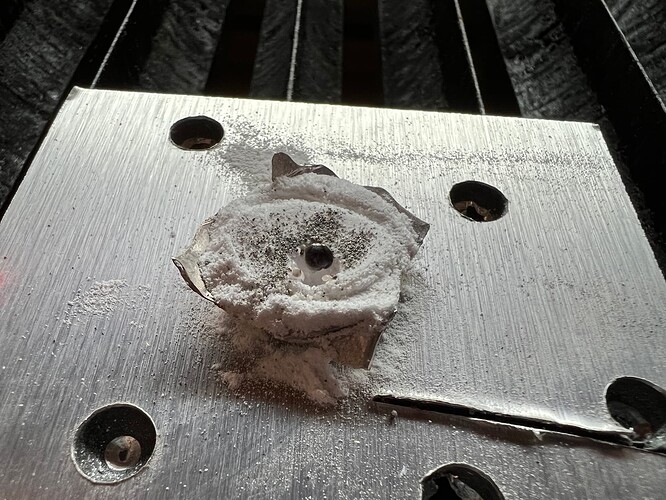
The result produced a single black sapphire and surrounding microcrystal of ruby.
After more runs I found that if I moved the laser head manually by a couple of mm whilst the aluminium oxide was still molten, I was then able quickly heat the surrounding powder and add to the previous crystal through coalescence. The coalescence was random and sometimes it contributed to the original crystal or it began forming a new one.
Once the aluminium oxide was hot enough I found it took very little to melt the surrounding oxide to the point I could now have a slow travelling beam.
So I adopted this 10mm square cut route. I set the laser to travel at 1mm/s at line intervals of 0.125mm.
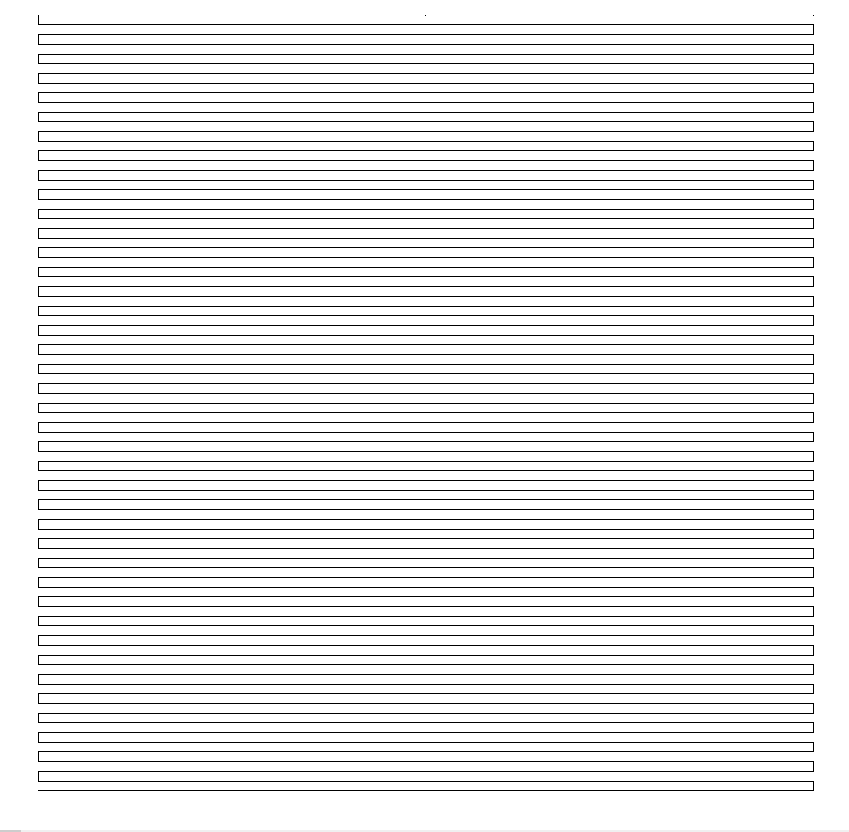
After a full pass I was able to gather a nice collection of rubies and sapphires.
I didn’t have time to get myself a sieve so the container contains some aluminium oxide powder as well.
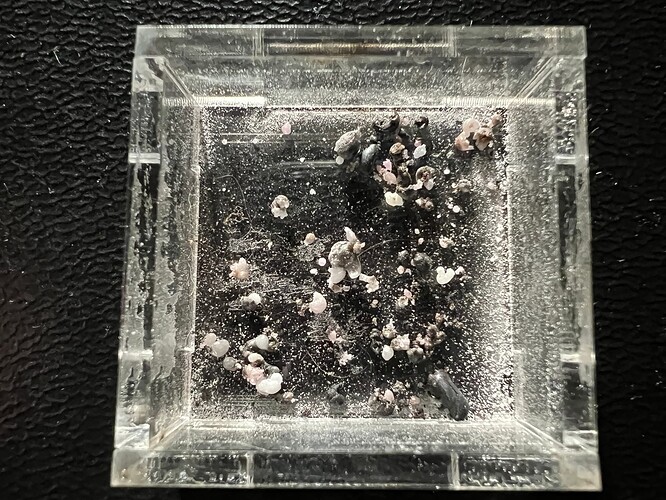
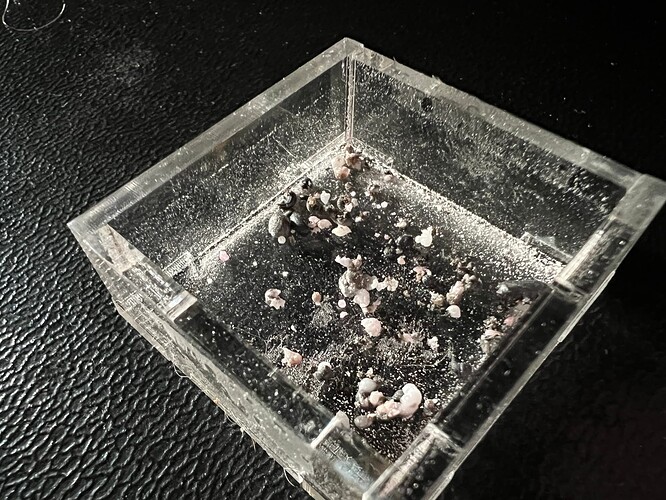
And now the fluorescence shots!

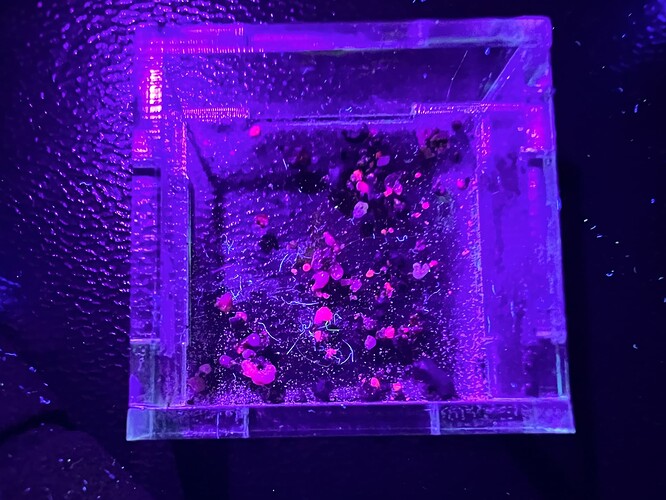
BA32DF41-15FB-490E-9F48-DE49D4D0E87A (1)1920×1440 235 KB
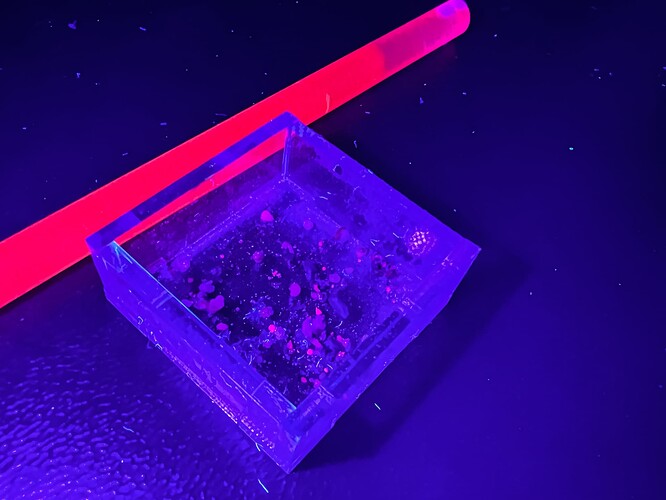
Using steel dust as a dopant produced some interesting results and potentially rare raw crystals. I have a couple of samples that have coalesced together containing ruby, clear sapphire and black sapphire. There also appears to be pale yellow variety present. I am yet to produce the classic blue sapphire.
To improve things further I am going to try a couple more things.
- Adopt a circular spiral cut route. This is to hopefully allow a singular central crystal to grow outwards.
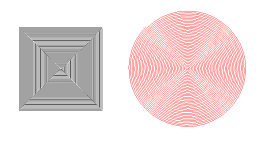
- Mix a higher concentration of steel dust thoroughly into the oxide powder. Hopefully stronger doping may occur. I saw some evidence in microcrystals that produced very red rubies.
- Potentially invest in pure chromium and titanium powders to try out creating higher quality and purer Cr:Al2O3 (Ruby) and Ti:Al2O3 (Titanium Sapphire) crystals.
- Produce crystals on a layer basis. I’ve proved I can remelt and coalesce the oxide horizontally so there should be no reason I can’t build on them vertically.
- Risk using small quantities of iron powder to see if I can make the elusive blue sapphire.
Edit:
Some closeups of some of the crystals.
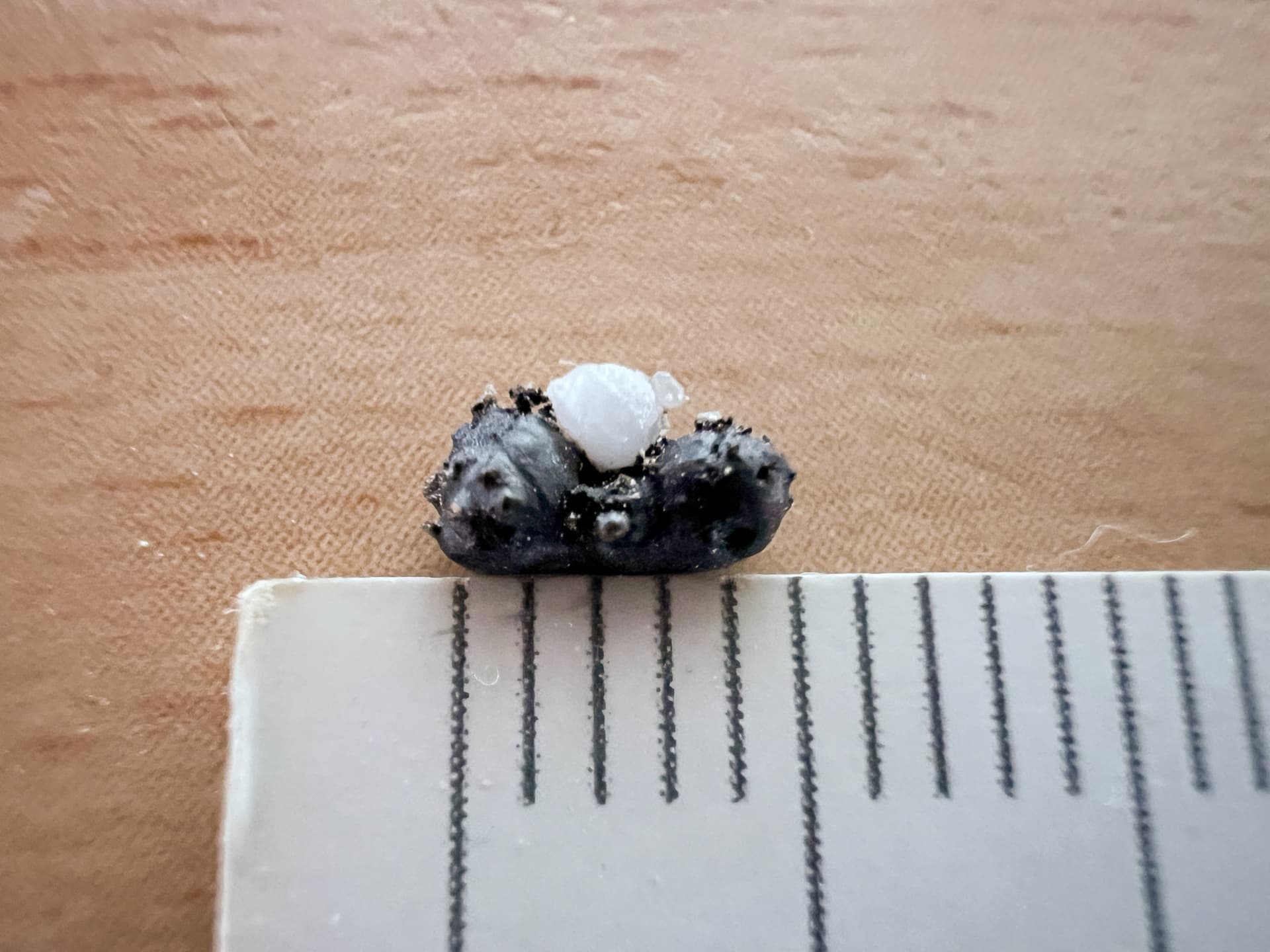
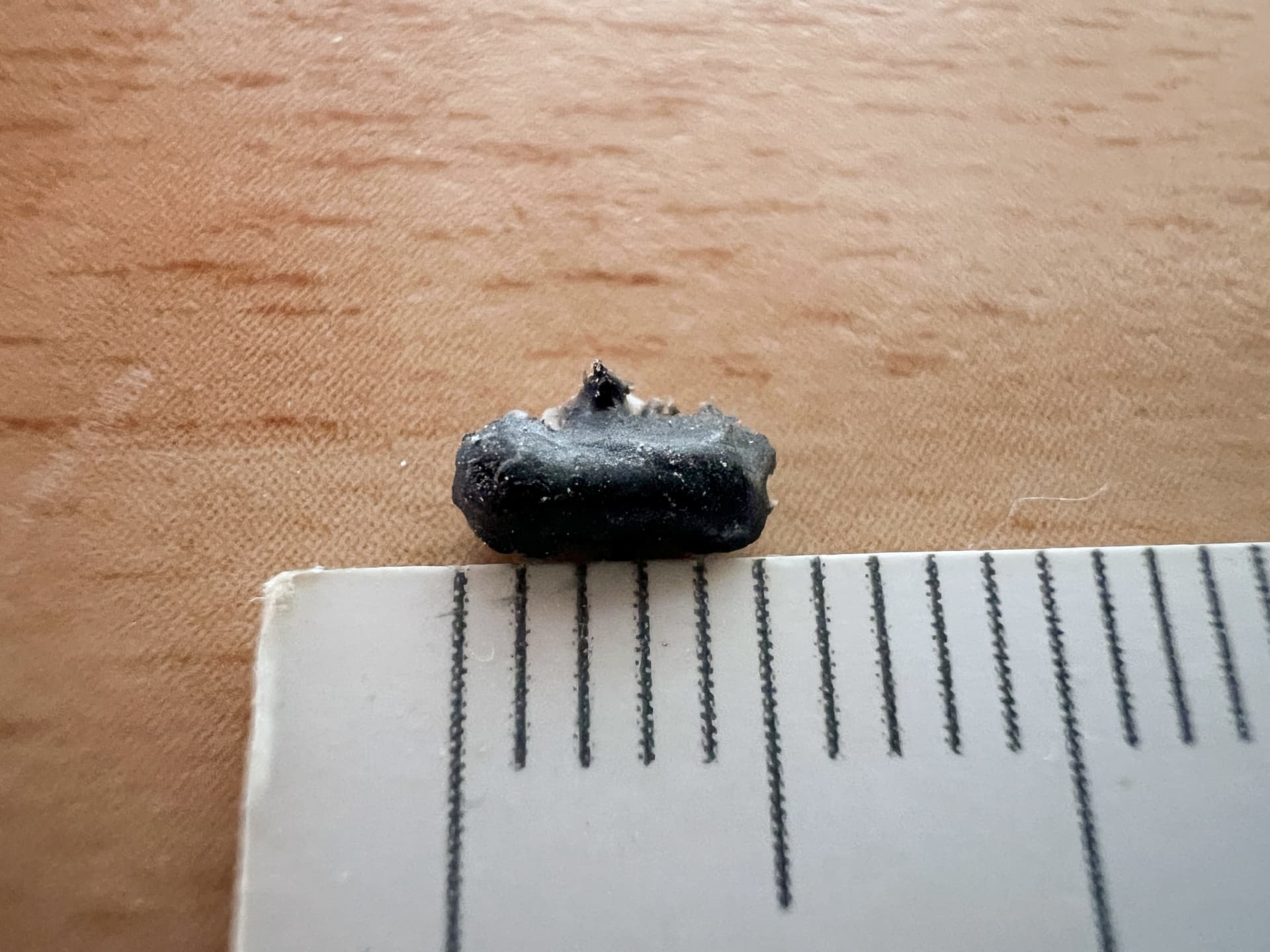
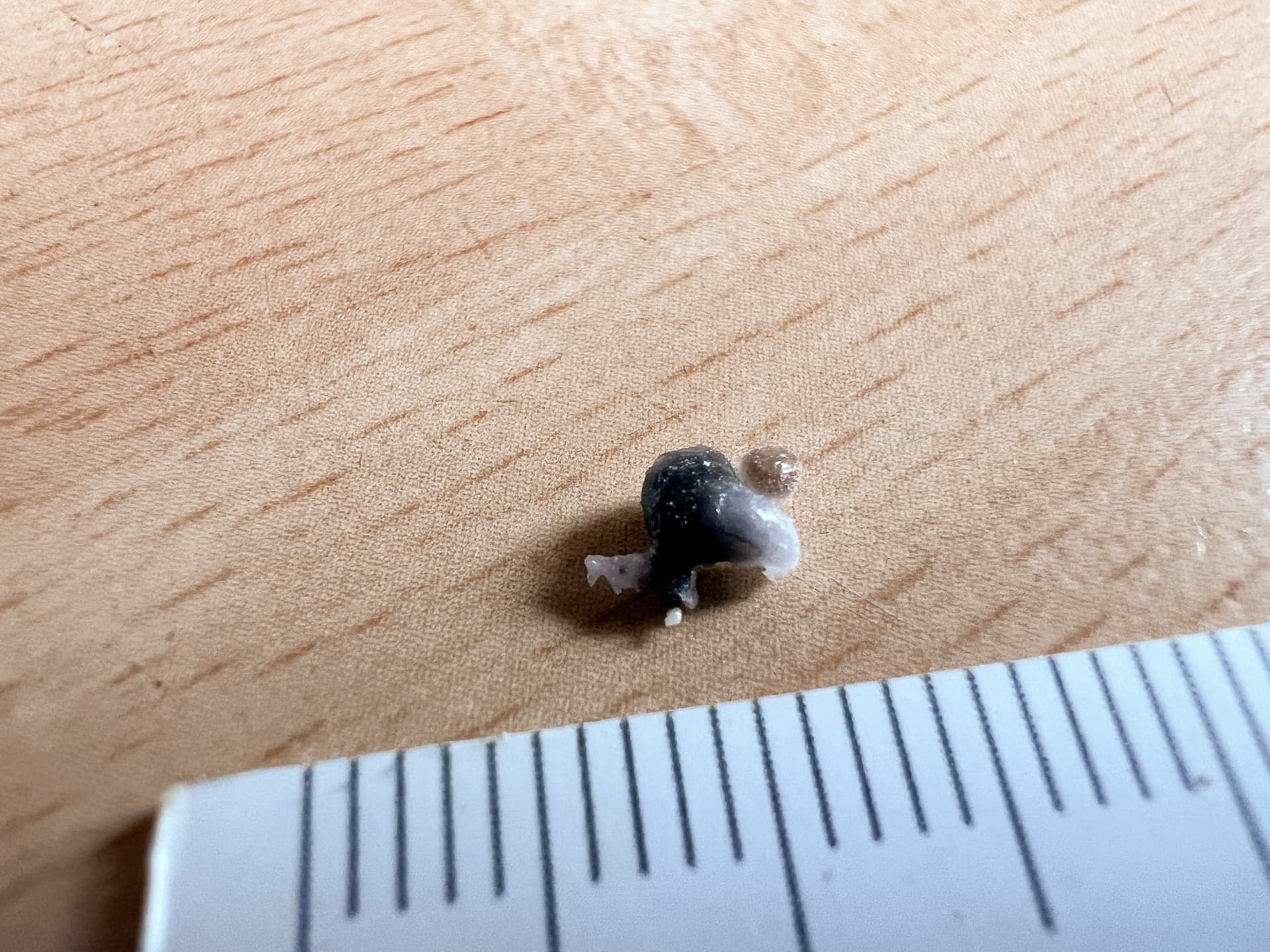
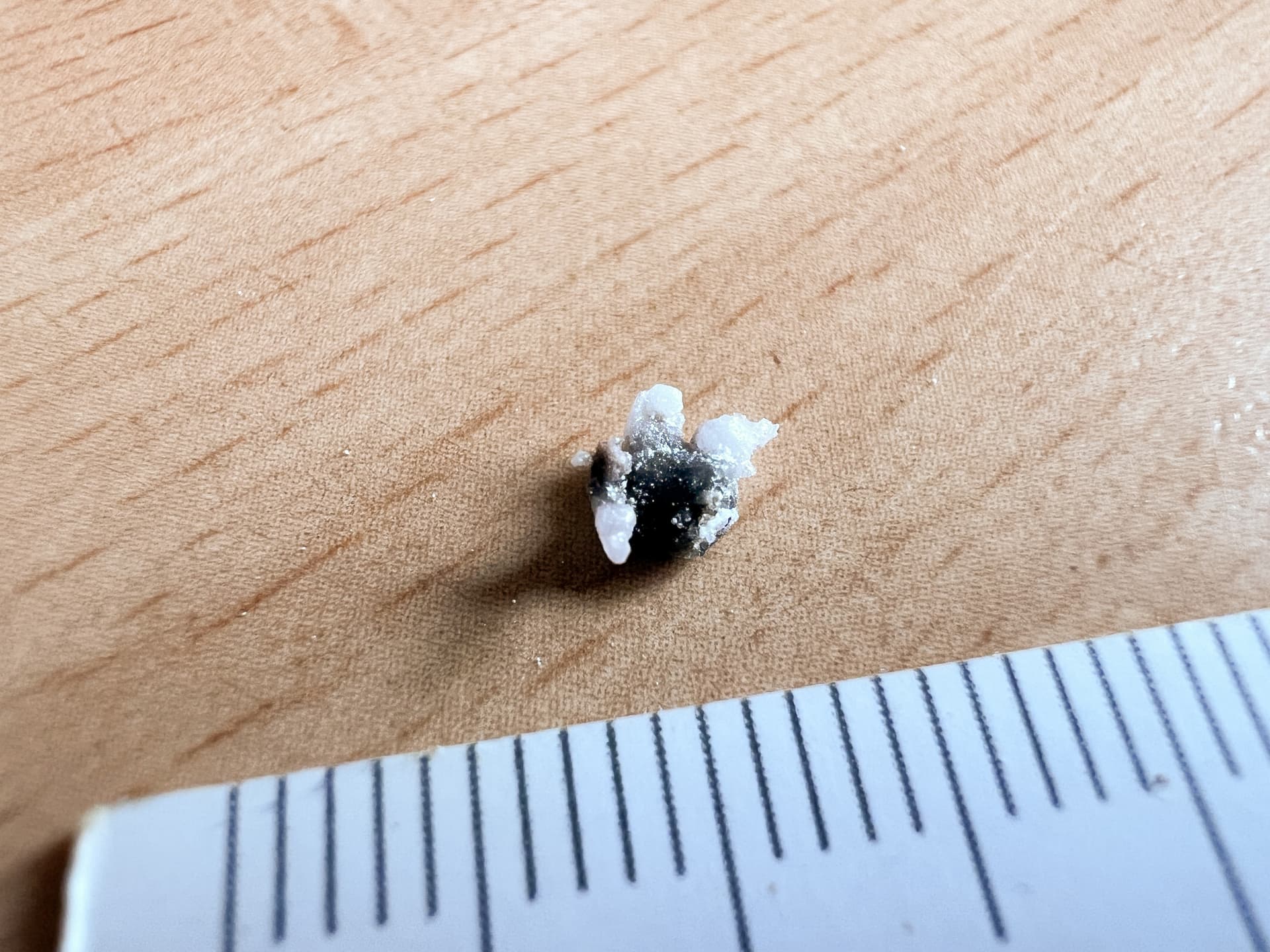
And under closer inspection I have discovered at least two microscopic blue sapphires.
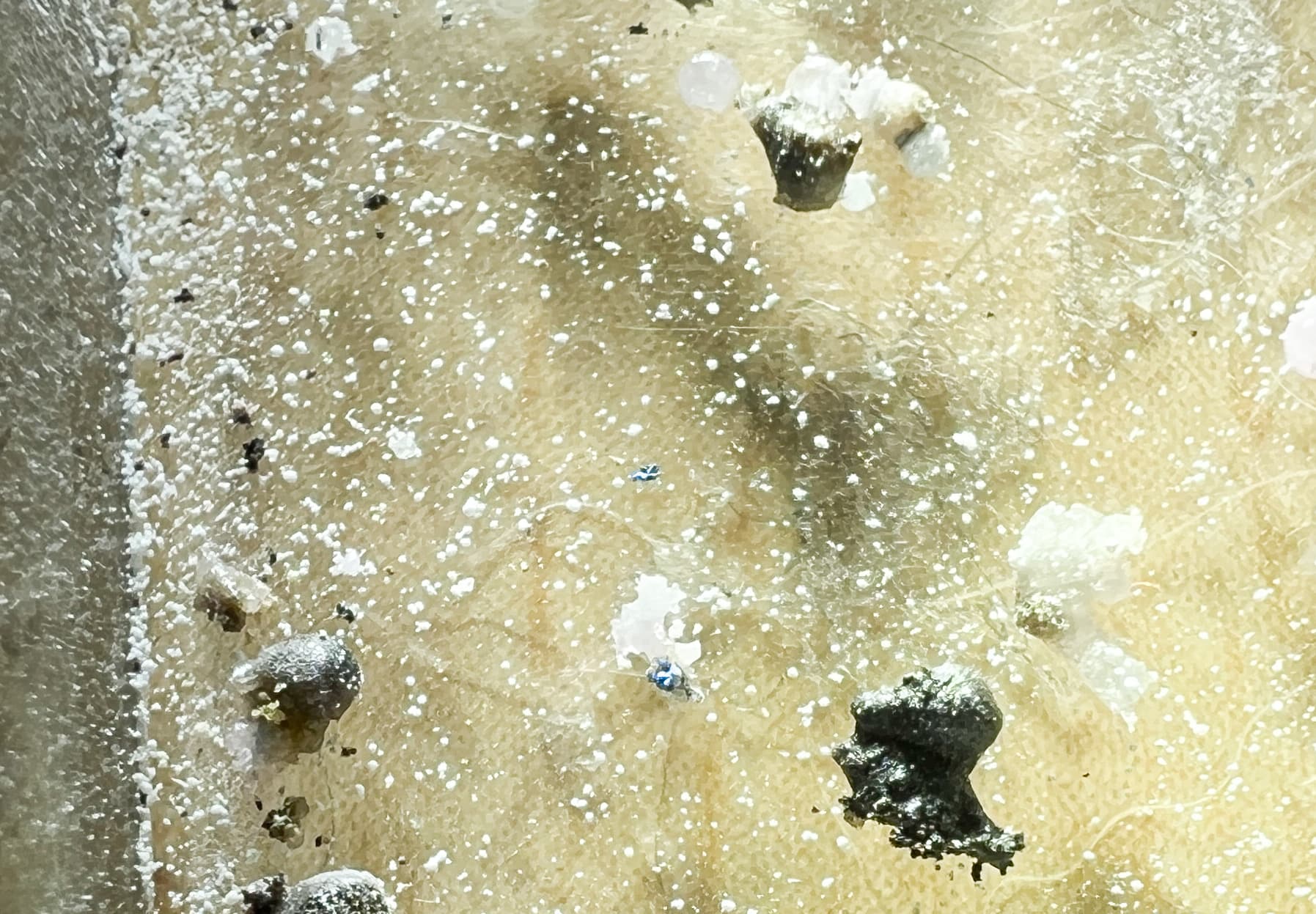
Note: The image has had to be altered to show the blue tint. It was very hard to capture it on my phone.
Last edited: