Hello Guys,
I am working on a new project.
Lets look into:
First of all, what's tiny RGB ?
Its a small single mode RGB laser pointer with beam correction, integrated battery and USB-C Charging port.
It got:
How tiny is tiny ? Take a look for yourself:
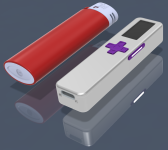
Lighter sized is tiny !
81,25mm long, 19,5mm wide, 12,5mm thickness.
Thats it for now, next posts will be the build log
I am working on a new project.
Lets look into:
tiny RGB
I already posted some teaser pictures in a different thread. Because some people have shown interest in RGB in general, I wanted to give you some sort of build log. It wont be complete but it will at least show progress.First of all, what's tiny RGB ?
Its a small single mode RGB laser pointer with beam correction, integrated battery and USB-C Charging port.
It got:
- 185mW 638nm / 120mW 520nm / 120mW 450nm Diodes - roughly 400mW of neutral white output
- tiny 1,5mm round output beam diameter with under 10mm beam at 10m distance - DPSS like
- 2Wh of integrated battery - good for roughly 45min of lasing at full output
- Full color Display and D-Pad as a userinterface
- Full analog modulation with 10bit color depth for amazing fades and colormixing
- configurable 5mW output limit - safe mode to use without goggles to enjoy the colors
- Over temperature protection for battery and laser diode safety
How tiny is tiny ? Take a look for yourself:
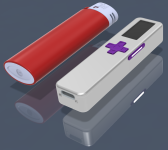
Lighter sized is tiny !
81,25mm long, 19,5mm wide, 12,5mm thickness.
Thats it for now, next posts will be the build log
Last edited: