Marecek
New member
- Joined
- Feb 2, 2020
- Messages
- 7
- Points
- 3
Hey, everybody,
This is probably my first post so I'd like to show my better side. I would like to show my latest project regarding lasers. It's a 520nm 750mW laser.
It is completely my design including 3D prints, switched CC converter and complete test and diagnostics. Before I get to the description of the CC converter though, it is an aluminum structure that serves as the heat sink and frame of the entire device. The 520nm TO9 laser diode is housed in a G2 lens optic and the whole thing is encased in a brass die. Hidden inside the green handle is a push button and a 3S LiPo 450mA/h battery (for models).
So, to get to the inverter, it is a switching step-down inverter with a current loop. It's designed to minimize ripple and protected so that in the event of a fault, the full battery current won't enter the diode. The control of the step-down converter I have 0 - 100% duty cycle. To protect the laser diode I have an integrated softstart with pushbutton input. The softstart is about 250ms long.
The switching power supply works from 7 - 20v and the output currents specifically for this piece I made 150 - 1900mA, but after changing the shunt you can go up to 20A.
So hope you like it and have a great rest of the day everyone. Regards Marecek
.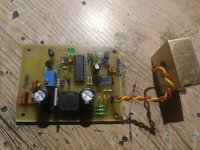
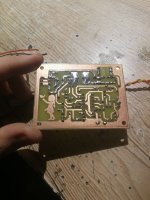
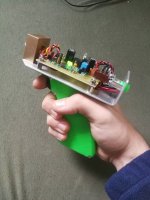
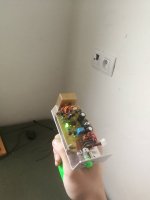
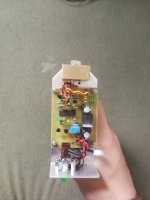
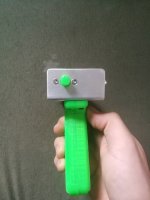
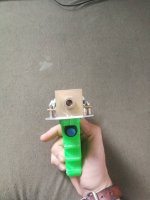
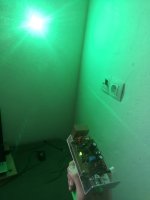
This is probably my first post so I'd like to show my better side. I would like to show my latest project regarding lasers. It's a 520nm 750mW laser.
It is completely my design including 3D prints, switched CC converter and complete test and diagnostics. Before I get to the description of the CC converter though, it is an aluminum structure that serves as the heat sink and frame of the entire device. The 520nm TO9 laser diode is housed in a G2 lens optic and the whole thing is encased in a brass die. Hidden inside the green handle is a push button and a 3S LiPo 450mA/h battery (for models).
So, to get to the inverter, it is a switching step-down inverter with a current loop. It's designed to minimize ripple and protected so that in the event of a fault, the full battery current won't enter the diode. The control of the step-down converter I have 0 - 100% duty cycle. To protect the laser diode I have an integrated softstart with pushbutton input. The softstart is about 250ms long.
The switching power supply works from 7 - 20v and the output currents specifically for this piece I made 150 - 1900mA, but after changing the shunt you can go up to 20A.
So hope you like it and have a great rest of the day everyone. Regards Marecek

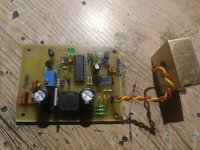
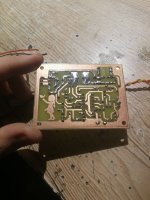
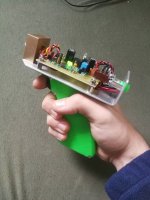
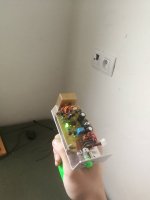
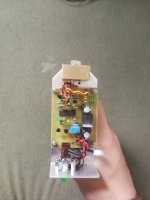
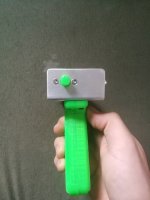
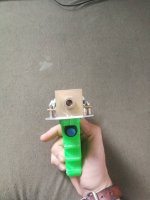
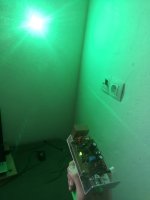